Concept to manufacturing ready drawings.
Taking a part or product from concept to manufacturing involves a number of steps.
The required functionality of the product must be defined up front. The
physical shape and feel (if that matters) are at least roughly defined. Environmental factors are considered -
temperature, dampness, impact, vibration and shipping among others.
It helps to have the purchased components - displays, switches, feet, handles, connectors - specified as early as
possible so openings, clearances, etc. can be worked out as the design progresses.
|
 |
|
|
What we Start With.
Part design can begin in a number of ways:
- a simple 'back of a napkin' sketch
- a whiteboard discussion in your office
- existing 2D drawings in either paper or electronic format
- existing 3D CAD documents
- a sample part or rough prototype
|
 |
|
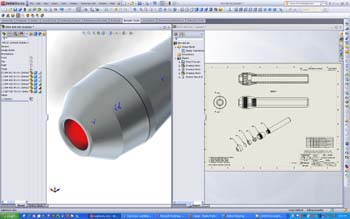
|
Build it first in a good CAD system.
The latest version of SolidWorks® is our CAD
system of choice. It is, in our opinion, the best tool around for designing parts and assemblies,
creating accurate fabrication drawings, Bills of Material, etc..
Integrated tools facilitate checking component sizes and fits, check for interferences, tolerance build up and
other issues before prototyping or manufacturing begins.
Accurate part and assembly weights, center of gravity and other useful information is tracked while the models
are being developed.
|
Sheet Metal Design:
Experience working in precision sheet metal shops has given us an understanding of
what can, and as importantly, can not, be formed out of metal.
Edge proximity, punch vs. metal thickness, bend allowances and bend radii are examples
of design parameters that affect part results and success.
If you have existing sheet metal vendors that you prefer to work with,
we can 'build-in' appropriate bend allowances for their tooling. Although there are
standard formulae for calculating these numbers, we know that some vendors have proven
out their own bend allowances, mostly for 90 degree bends, based on tooling and experience.
Many vendors include some measure of time to program flat patterns in their part cost
quotations. We can supply flat patterns to them, thus reducing your costs.
|
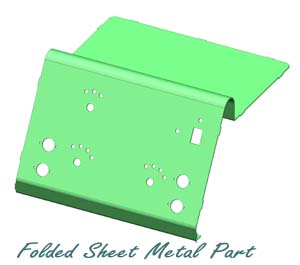
|
|
Machined Part Design:
Again, experience working in metal shops has provided a
good understanding what it takes to turn and mill metal and plastics.
We work with local machine shops, or your existing machinist, to avoid difficult to machine
features and features requiring special tooling.
Cutter run outs, deep small radii, drafted surfaces, small holes and material warpage
are among the items that must be watched and controlled.
Tolerancing of machined parts can be critical, so special attention is paid to running or
interference fits and sliding surfaces. This is true of surface finish (roughness) also.
|
|